The advantage of permanent magnet is to offer a stable regulation of basins. The technology connected to the system is also simple and intuitive.
“This motor technology, which is directly coupled to the propeller (i.e. without a gearbox), met all our requirements in every respect: less energy-consuming motors and much more precise airflow control. It was the deal solution to our mechanical problems and tour our recurring control and maintenance operations.”
Gérard DANDEVILLE, Maintenance Manager, Operational Unit CDGL
ADP manage its own energy and cooling production for airports.
“The specifics of our process regulation caused recurring mechanical failure problems in our motors with reduction drives installed on our cooling towers.
We identified the cause of these repeated failures:
The speed inverter coupled with a standard motor equipped with a reduction drive caused overheating when our process required ventilation with a slowly turning propeller.
In order to avoid motor overheating, we have defined the inverter’s operating range between 22 and 50 Hz. Below 22 Hz, the system went into standby mode.
During this shutdown, the oil contained in the reduction drive went down to the bottom of the sump. At the time of an automatic restart at 22 Hz, the reduction drive gear lubrication was no longer sufficient, causing the mechanical failure of the reduction drive.
The loss of functions of the two cold groups due to the failure of the cooling towers (7 MW per cooling tower), which was happening two to three times a year, became very problematic for our production.
In addition, we had to deal with increasingly significant maintenance costs at each shutdown of our towers: 15K€ in spare parts and maintenance costs.
Permanent magnets ensure stability in energy and cooling system
At a meeting with Ms. RATEAU, Renovation & Environment Service Manager at JACIR, during a trade show we learned about an alternative to the motor with reduction drive technology aimed at eliminating the reduction drives, a solution which we considered to be an exact answer to our problem.
JACIR then suggested its design to us involving the replacement of the current motors with reduction drives by permanent magnet motors coupled with WEG brand inverters, highlighting the following 4 ways to make improvements:
- Regulate the cold water temperature off-season and operate in the previously unattainable range of 0 to 22 Hz,
- Communicate with our GTC by the Ethernet protocol,
- Reduce maintenance operations and costs,
- Meet the new standards concerning energy efficiency for motors.
This motor technology directly coupled with propeller (thus eliminating the reduction drive) met all of our requirements: the motors with a lower energy consumption and a much more precise aeraulics regulation.
This seemed to be the ideal solution for resolving our mechanical problems and our recurring inspection and maintenance works.
A complete analysis of the tower structure was carried out by JACIR to ensure the adaptability of the proposed solution.
A new motor support (frame and chassis) was made of stainless steel 316L to conform to our water treatment procedure, which is essential for Legionella measures.
In order to obtain a complete picture of potential solutions available in the market, we consulted other companies, but none was able to propose another solution which includes all these advantages nor expertise for fitting new motors that appeared to be reassuring as that of JACIR.
After visiting other sites on which JACIR teams had carried out this installation, we were reassured with very good feedback from operators: JACIR-WEG technology is reliable and offers a significant decrease in electricity consumption.
The JACIR team has managed turnkey planning and execution to install the motors.
Once the motors were delivered by WEG to a JACIR facility, they were prepared and factory installed on their support, with only the blades remaining to be assembled on site.
This preparation made it possible to perform the installation in one day for each cooling tower, which we considered overly optimistic when JACIR presented us with their time frame. We must admit that JACIR has delivered on the committed deadlines.
Since the installation of the permanent magnets motors, we established that it was no longer a challenge to regulate the reservoirs and the temperature remained constant.
We are now using ranges of between 0 and 50 Hz and 0 to 380 rpm without any concerns.
We also noticed a net decrease in the noise from cooling towers and from vibrations, while the structure of the tower is no longer experiencing jolts during start-ups or rotation speed accelerations of the propeller.
We were pleasantly surprised by the simplicity of use of the speed inverters.
Implementation of the programming technology:
To support our teams in charge of the regulation, which were very reluctant at the beginning to change inverter brand, JACIR and WEG offered us training during the commissioning of our equipment.
Setting up the parameters and training our teams took place following the assembly operations and everything was very simple and in French, which we appreciated.
Following this training, our teams found that the newly implemented technology was very easy to use, very user-friendly and above all, very intuitive.
Not once did we have to intervene in the programming set at the beginning.
We appreciated the partnership between JACIR and WEG who supported us on this project from analysis through to its realisation.
It was a business well done, completed on schedule, and really improving our thermal efficiency: we estimate that our annual consumption budget has now reduced by half.
We would not hesitate to recommand the JACIR-WEG PERMANENT MAGNET MOTORS solution for their excellent technical support and turnkey installation completed on schedule.”
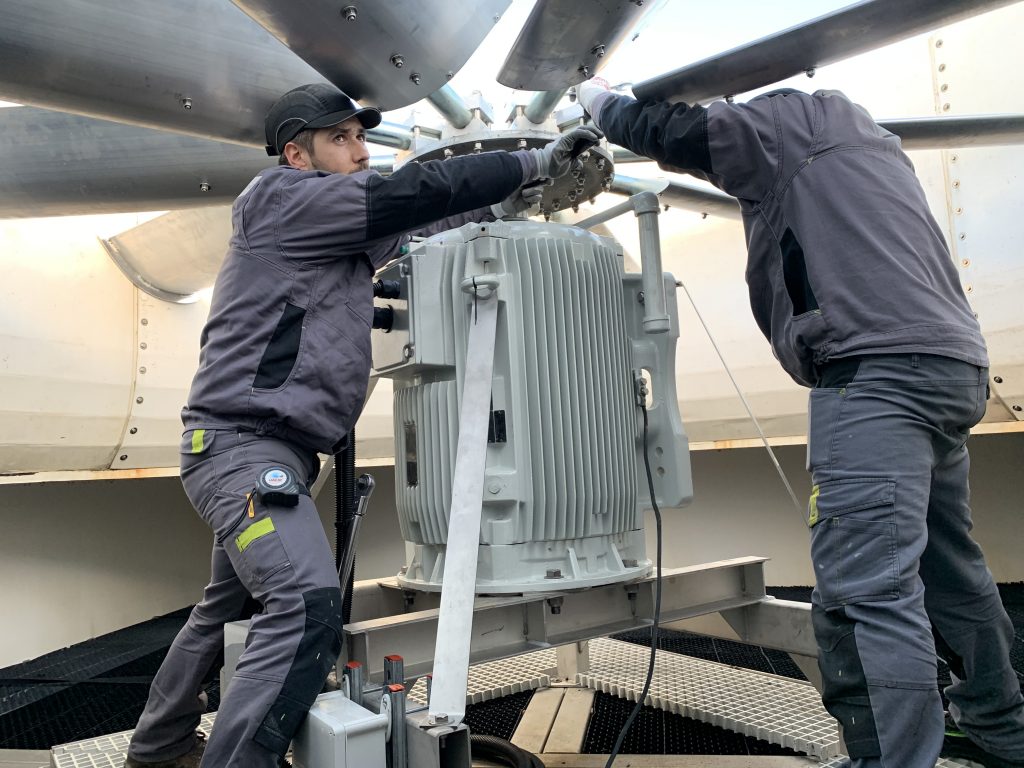
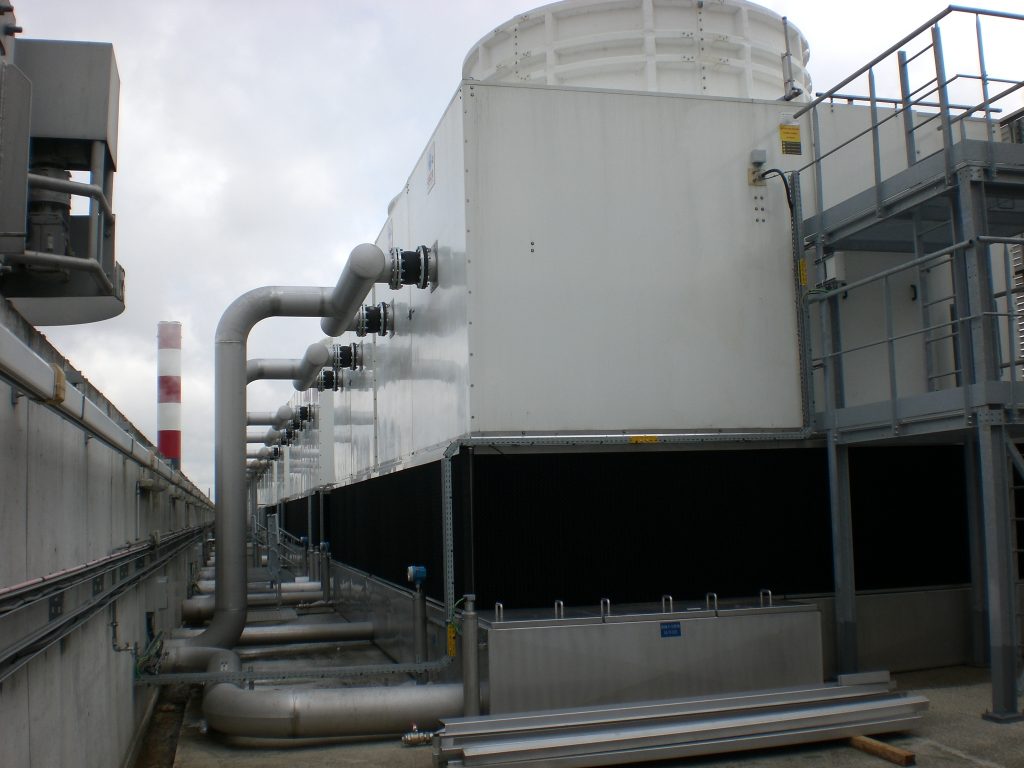
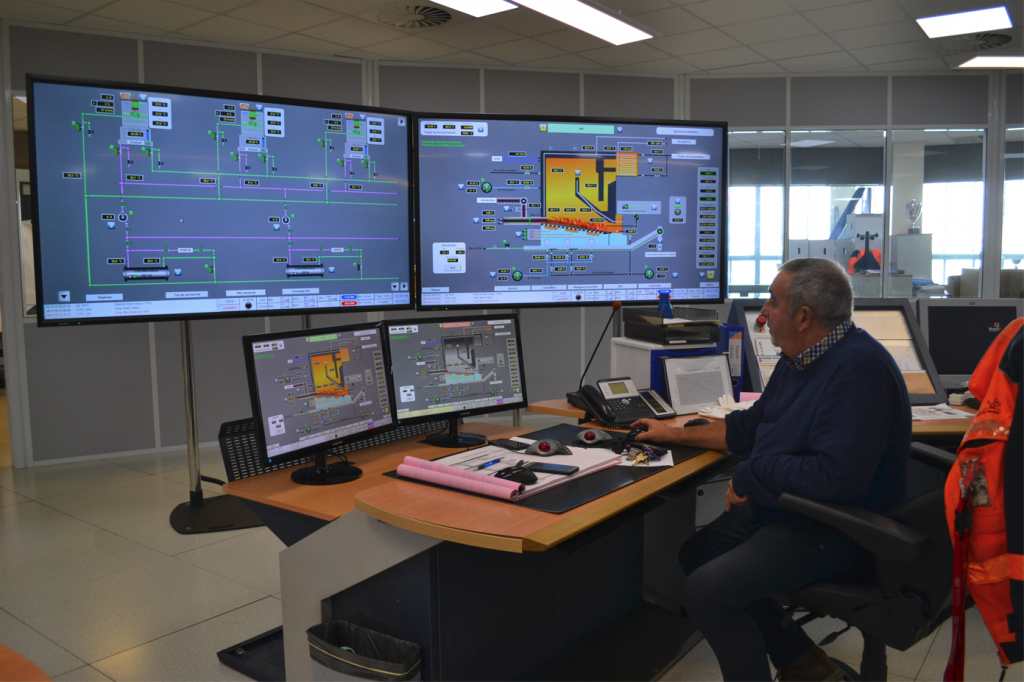